Optimize Automotive Manufacturing with Cutting-Edge Metal Stamping Techniques
Metal stamping is a highly efficient process that employs stamping presses and dies to shape metal sheets into the desired form. Renowned for its efficiency, this process is acknowledged for producing complex parts with tight tolerances and specifications, ensuring optimal repeatability. Metal stamping has become an indispensable element in the automotive industry, particularly for electric vehicle (EV) manufacturing.
Automotive metal stamping has gained popularity within the EV sector due to its prowess in crafting intricate, lightweight components that effectively reduce fuel consumption and carbon emissions. EV stamping is also a solution for producing parts with optimal material efficiency and cost-effectiveness. At ESI, we comprehend the challenges faced by our automotive customers and provide a range of manufacturing services and engineering solutions, including cutting-edge Geocomposite capabilities, aligning with the industry’s stringent requirements. Using the latest automated systems, we efficiently deliver safety-critical EV parts with optimal speed and quality.
Advantages of Utilizing EV Stamping in the Automotive Industry
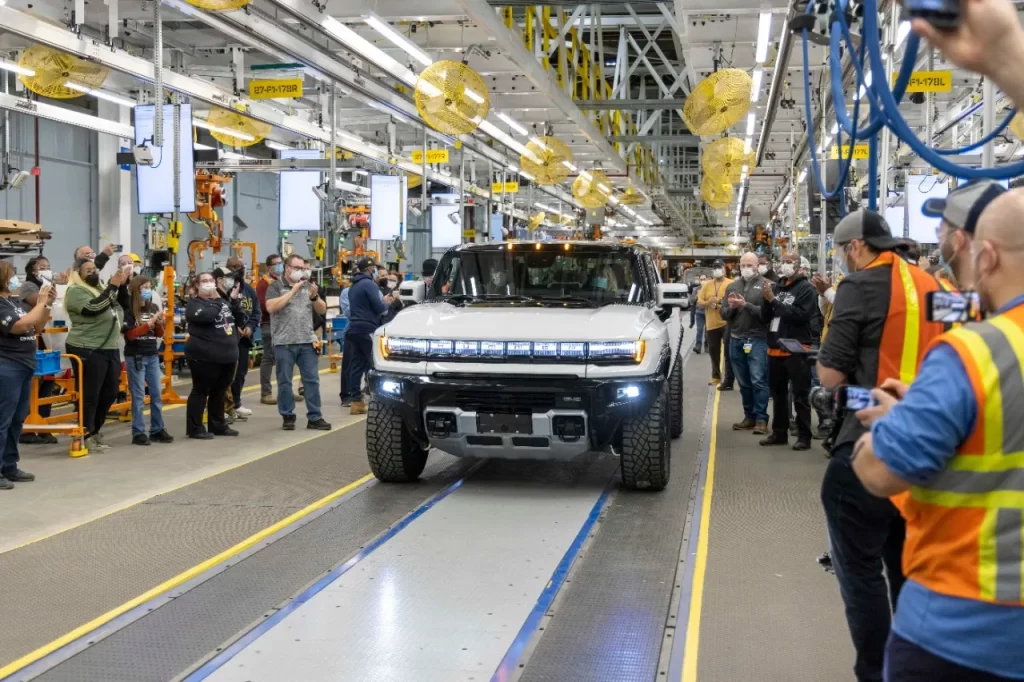
Our EV Metal Stamping Capabilities
At ESI, our comprehensive metal stamping capabilities for electric vehicles, encompass:
- Punching: Used to cut holes into the metal workpiece, with the punched material typically becoming scrap.
- Blanking: This involves cutting material from a metal sheet into the desired shape, creating a new blank or workpiece.
- Embossing: Presses a die into the metal, creating a raised or recessed design.
- Coining: Applies high force to make the workpiece conform to the shape of the die.
- Bending: Uses a die to form the metal workpiece into specific bend patterns, such as V-shape or L-shape.
- Flanging: Bends the edge of the material to create a flange for connecting components.
Tailoring these processes to your needs allows us to efficiently produce the EV parts you require.
EV Stamping Industry Applications
Metal stamping is prevalent throughout the EV industry, manufacturing highly precise components adhering to strict design parameters and compliance regulations. Our Geocomposite capabilities make EV stamping processes incredibly versatile, enabling manufacturers to produce a wide range of parts in nearly any size. Common applications of EV metal stamping include A-frames, battery trays, body-in-white (BIW) components, brackets, brake parts, EV battery parts, EV charging parts, floor panels, heat shields, seating components, and transmission systems.
Advantages of EV Stamping
EV stamping offers automotive manufacturers several benefits, including automation that enhances safety, reduces errors, and increases production volumes without substantial labor investments. Additionally, EV stamping processes maximize material efficiency, utilizing workpiece material with minimal waste, and rely on cost-effective dies for maintenance after initial production, facilitating high-volume, cost-effective part production.
Initiate Your Next EV Stamping Project with ESI
EV stamping is a cost-effective and efficient solution for producing precise, high-quality components that meet the automotive industry’s strict requirements. At ESI, our reliance on progressive and four-slide stamping techniques, coupled with advanced Geocomposite capabilities, allows us to create safety-critical components from a broad range of materials. Utilizing cutting-edge automation with in-vision inspection, we consistently deliver finished products with unparalleled quality and accuracy.
For more information about how our metal stamping capabilities, including Geocomposite expertise, can meet the needs of the automotive industry, contact us or request a quote today.